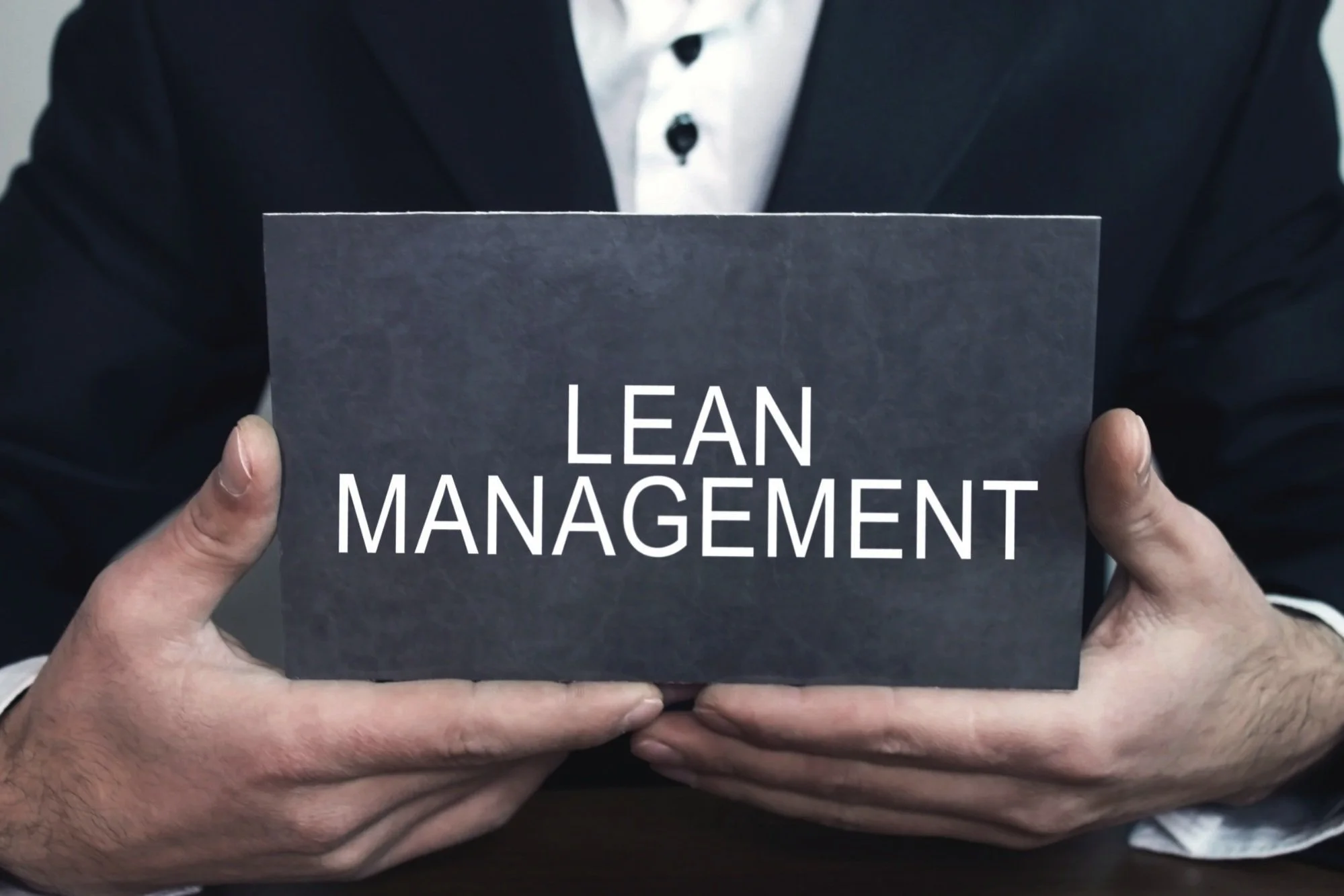
Lean Management
Employee Training - 5S Principals
5S Principles, derived from Japanese terms seiri (Sort), seiton (Set in Order), seiso (Shine), seiketsu (Standardize), and shitsuke (Sustain), are foundational to Lean Management and workplace organization. Our comprehensive 5S training equips participants with the knowledge and skills to transform their workspaces into organized, efficient, and visually controlled environments.
Sort (Seiri): Participants learn to declutter and streamline their work areas by applying the 48-hour rule. They identify and remove unnecessary items, tools, or materials, keeping only what is essential for their tasks. By reducing clutter, employees can optimize space utilization, minimize distractions, and improve workflow efficiency.
Set in Order (Seiton): In this step, participants establish a systematic layout for their workspaces, ensuring that everything has a designated place. They organize tools, equipment, and materials based on frequency of use, making it easier to locate and access items when needed. A well-organized workspace promotes productivity, reduces search time, and minimizes the risk of errors or accidents.
Shine (Seiso): The Shine step focuses on cleanliness and maintenance, encouraging participants to conduct regular cleaning and inspection activities. Through deep cleaning initiatives, employees not only remove dirt, dust, and debris but also identify and address potential safety hazards or equipment issues. By fostering a culture of cleanliness and accountability, organizations can create safer, healthier, and more pleasant work environments.
Standardize (Seiketsu): Standardization involves establishing protocols, procedures, and visual controls to sustain the improvements achieved through the first three S's. Participants learn to develop standardized work practices, visual management tools, and checklists to maintain orderliness and consistency in their work areas. Standardization promotes efficiency, reduces variability, and fosters continuous improvement efforts across the organization.
Sustain (Shitsuke): Sustaining the gains made from implementing the 5S principles requires ongoing commitment and discipline from all employees. Participants learn the importance of regular audits, training, and continuous reinforcement to uphold the standards established through the previous steps. By integrating 5S principles into daily routines and company culture, organizations can achieve long-term success in maintaining a lean, efficient, and high-performing workplace.
Our 5S training empowers employees at all levels to actively participate in the continuous improvement process, driving positive change and fostering a culture of excellence within the organization. Partner with us to unlock the full potential of Lean Management and transform your workplace for enhanced productivity, safety, and quality.
Inventory Management
Effective inventory management is crucial for businesses to maintain optimal levels of stock while minimizing costs and maximizing efficiency. Three common inventory management strategies are widely used in the manufacturing industry:
Pull Strategy: Also known as a demand-driven or just-in-time (JIT) approach, the pull strategy focuses on producing goods based on customer demand. Inventory is replenished only when it is needed, reducing excess inventory levels and minimizing storage costs. By synchronizing production with customer demand, businesses can minimize waste and improve responsiveness to market fluctuations.
Push Strategy: In contrast to the pull strategy, the push strategy involves forecasting demand and producing goods based on these forecasts. This approach often results in higher inventory levels to meet anticipated demand. While the push strategy can help ensure product availability and reduce lead times, it carries the risk of overstocking and increased carrying costs if demand does not meet expectations.
Just-in-Time (JIT) Strategy: JIT is a lean manufacturing principle focused on minimizing waste by producing goods only when needed and in the exact quantity required. JIT aims to eliminate excess inventory, reduce lead times, and improve production efficiency. By synchronizing production with customer demand and implementing efficient supply chain management practices, businesses can lower inventory holding costs and improve cash flow.
Each inventory management strategy has its advantages and challenges, and the most suitable approach depends on factors such as product demand variability, lead times, and production capabilities. At SMB Accounting & Consulting, we provide expert guidance on implementing the right inventory management strategy tailored to your business needs. Our comprehensive solutions help optimize inventory levels, reduce costs, and improve overall operational efficiency. Partner with us to streamline your inventory management processes and drive sustainable growth.